I. INTRODUCTION
In order to secure the world’s best competitiveness through innovation in manufacturing, Germany is promoting it as a national project called ‘industry 4.0’. Korea is also pursuing innovation in manufacturing by carrying out government-level projects of ‘Manufacturing Innovation 3.0’. In order to realize the innovations of this manufacturing industry, the logistics field is based on the internet of things (IoT) technology, and the project of ‘Logistics 4.0’, in which the latest technologies are fully applied, Should be equipped. In order to achieve this logistics 4.0, the logistics center which plays the role of the heart should be innovated first and the government-wide ‘Logistics Center 4.0’ policy should be boldly promoted.
Logistics Center In the age of 4.0, we collected all the information of the logistics center based on IoT, analyzed it by utilizing Big Data technology, and stored and transported the product based on the analyzed knowledge. : Artificial Intelligence) technique, and smart logistics center system that processes automatically by using robot. Logistics Center 4.0 The smart logistics center in the age of five must be technological innovation in the following five areas. First, it should have an infrastructure system based on IoT center that can collect all information automatically. Environmental information such as temperature, humidity and vibration in the logistics center should be collected in real time and transferred to the central operating system. The location and unique information of the products and the location and status information of the transportation equipment and workers can be monitored in real time. IoT based sensors and recognition devices must be developed. Second, robots and automation equipments that can efficiently perform storage, transportation, unloading, packing, and delivery of the unique functions of the logistics center are needed. Recently, it is necessary to develop a robot-based unmanned transportation and unloading system and an automatic packaging system as Amazon’s Kiba robot is utilized to efficiently perform storage and picking. To do this, we must develop a system that recognizes various kinds of unstructured products by utilizing soft computing and AI technologies. It is also necessary to research and develop methods to utilize unmanned vehicles and robots in order to deliver products efficiently and efficiently to customers at distribution centers like drone. Third, we need to build a Warehouse Management System (WMS) system for optimized logistics center operation. This requires a smart operating system that can optimize and efficiently manage all the series of processes, including robots and automation equipment, using AI techniques and big data technologies. To do this, we collect and analyze all the fixed and unstructured data obtained from the IoT sensor-based infrastructure system to visualize and optimize the whole process and operation information based on the Big Data and AI, and to develop the technology to proactively diagnose and diagnose faults and risks need. It will also support enhanced services based on cloud and mobile capabilities. Fourth, interface equipments that enhance safety and efficiency of logistics center workers and realistic work management system are needed. Based on virtual reality (VR) and augmented reality (AR) technology and indoor location tracking technology, it assists workers in on-site work and improves efficiency and secures workers’ safety. Work-assist systems such as wearable robots have also been developed for unloading and transporting heavy-weight unstructured products that require manual operation.
In addition, a sensible task management system that provides visibility using wearable devices such as smart glasses should be developed to manage all robots and automation equipments in real time in the field. Fifth, eco-friendly logistics center design technology that can apply flexible logistics process is needed. In order to apply the efficient arrangement of various robots and workers including drones and the flexible logistics process, the fixed logistics facilities are replaced by the flexible and flexible assembled modular logistics facilities and changed from the planar layout to the three dimensional spatial layout. In addition, a structural redesign is required for logistics centers based on 3D printers, where manufacturing and logistics are performed at the same time, and an eco-friendly energy system in which energy consumption is automatically optimized will be applied. Future smart logistics center technology will be developed and applied through the implementation of ‘Logistics Center 4.0’ policy in the future. It is also expected that manufacturing innovation will be possible.
The smart logistics center greatly reduces the space for storing goods and manpower, and it enables to promptly perform goods receipt, warehousing and inventory management by reason of information processing system, so that surplus inventory and regular inventory can be always grasped in real time So that the manager can promptly judge and take action to prevent property loss due to unused inventory. In addition, it is possible to integrate various warehouses distributed in the factory to enable compartmentalized and batch management, to replace the transfer facility with automation equipment, and to manage the I / O and inventory management including products and raw materials through information system (ERP: Enterprise Resource Planning), which is a superior management information module.
These technologies have long been used to store raw materials and to store manufactured parts and semi-finished products in the general assembly industry as well as logistics centers, and are usually used by crane operating along a passage between the racks.
In particular, smart technology has been developed and commercialized in many industries in recent years due to various complex factors and characteristics of a wide variety of changes. The key point of the unmanned landing system is to automatically manage and manage the barcode, RFID (Radio Frequency Identification) technology, shape recognition technology, and unmanned crane control technology in the smart logistics center. It is a created WMS system.
In the case of a stacker crane used in a conventional automatic warehouse, a telescopic fork was mounted on the "lifting device" for carrying the product, and only one product could be stored in one row of the stacker crane left and right racks while the fork was moved forward and backward. In order to recognize the position of the pallet autonomously, a laser scanner having a two-dimensional detection range is installed on the fork carriage to scan the pallet hole.
However, since the operation of the automatic warehouse for logistics up to now is centered on the stacker crane, it is not only low in reporting and efficiency, but also increasing the economic burden due to the increase of facilities. It is not properly managed. In order to solve this problem, the concept of shuttle has been introduced to improve the storage efficiency of the automatic warehouse in recent years. Some papers proposed the path decision method based on intelligent algorithm based on the CPS logistics path decision model, the Internet of Things technology and cloud platform data storage technology are introduced into the interconnection design and data processing of the equipment layer.
It is an automatic warehouse facility using one shuttle, stacker crane or satellite and it is a logistics automation system which has a saving of 50% in frost amount and 60% increase in storage compared to the existing automatic warehouse system. By introducing a new device called shuttle, which is a facility to transport products horizontally, it is possible to report multiple products in one row unlike the existing stacker crane equipment that only stores one product in one row of storage racks. Conventional stacker crane frame is used as it is, but concept of product storage and operation of warehouse are different from existing facilities by adopting elevator, shuttle, instrument control, product storage rack and operating software. However, the research on the operation management system including the shuttle is insignificant. Therefore, in this study, in connection with a mobile robot device called “shuttle” and an automation device of “stacker crane” or “satellite (or radio shuttle)”, We propose Warehouse Management System (WMS) for automatic operation of the system. It automatically collects barcode or RFID information attached to the pallets required for warehouse automation and automates both goods receipt and warehousing in a way that interoperates with shuttle, stacker crane, or satellite, It is a system that can solve unattended automation operation.
II. SMART TECHNOLOGY OVERVIEW
The word “smart” is the word most commonly used in many mediums that we have recently encountered. Recently, we have been able to easily access smart technologies by watching products (Smart Phone, Smart TV, Smart Grid, Smart Key) that contain the word smart in our society. Smart technology is not technology itself, but technology that makes individuals and industries smarter. Smart technologies to provide personalized products and services that can sensitively recognize situations occurring everywhere and respond quickly through analysis and forecasting can be classified into three categories: Sensing, Intelligence, Mobility, Elasticity), And Integration (Integration). Techniques such as artificial intelligence, object internet, big data, drones, 3D printers, and beacon / Near Field Communication (NFC), which are developed through these exclusive and complementary properties, . Smart technology will serve as a driving force to create new businesses for each industry and to continuously evolve and develop. In addition, a number of smart technologies have been applied to industrial areas, leading to changes in new industries that were not possible or impossible in the past. Figure 1 shows the size of the domestic Internet market.
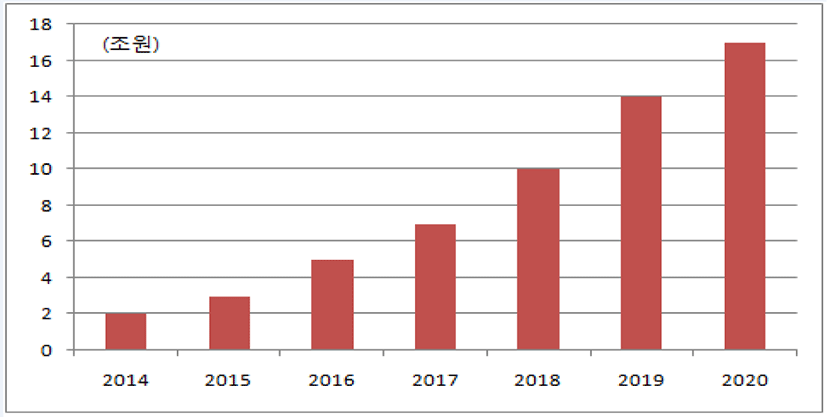
The development of smart technology has opened a variety of possibilities beyond conventional business manufacturing, which has been mainly used in the assembly process. In 2012, Amazon acquired a robot developer, Kiva System, which released a warehouse management robot rather than a assembly process. Kiba robots are currently being used to locate and ship inventory to the massive warehouse in Amazon, to find and ship the goods, and to sort out popular and ineligible products and relocate them in the warehouse. Kiba robots show a 20% ~ 40% improvement in work efficiency compared to humans.
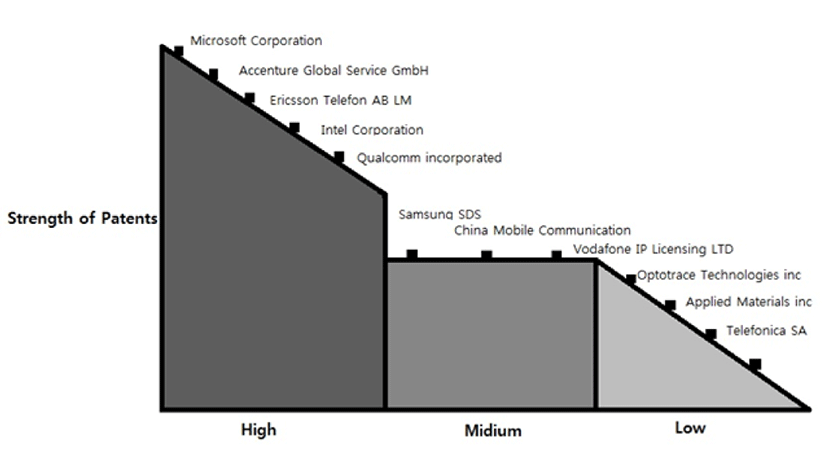
In addition, emerging countries such as the US, Germany, and Japan are showing signs of revival in the manufacturing industry. For example, in the recent declining US automotive industry competitiveness, Tesla Motors, a California electric car maker, is growing rapidly and growing its US manufacturing base. Tesla Motors, a manufacturer of high-end electric cars powered by 100 percent, has a workforce of 160 robots and 3,000 workers at its California plant.
III. LOGISTICS CENTER DEFINITION
The Physics Distribution Center refers to the logistics hub and facilities that perform the functions of unloading, storage, warehousing, and delivery while keeping inventory in order to provide services for customer orders. In addition, in order to integrate and plan the efficiency of the distribution process of products in which there are a plurality of suppliers and consumers, it is installed between the supplier and the consumer so as to improve the efficiency of the shipping. The center will be responsible for replenishment of goods. In Korea, the term “logistics center” has been used since the late ‘90s, but the formal definition and legal standard of the logistics center is insufficient to date. In Korea, it was used as a warehouse rather than a logistics center. It was used until the early 90’s. The definition of the Freight Distribution Promotion Act is “Warehouse is a land or a sleeping area to prevent loss of work and goods to prevent loss or damage of goods. To be used to store the goods”. Generally, the distribution center delivers goods to customers according to the order of the consumer (customer, retailer, company).
The logistics center plays a coordinating role between manufacturing and sales, and functions to adjust the supply and demand according to the discrepancy in demand. Specifically, there is a time difference in demand for manufacturing and sales, a spatial difference according to the location of factories and retailers, a quantitative difference due to differences in production quantity and sales quantity, a uniform quality maintenance for the same distribution product, And to overcome the quality difference for the same quality preservation at the time of sale. Typical logistics functions at the logistics center include the following functions. In other words, inventory management functions such as ordering and ordering functions, inventory management, order forecasting, distributing processing of distribution processing and packing tasks, input / output work, storage work, picking work, Maintenance functions such as loading / unloading of transportation works, maintenance of buildings, maintenance / regular inspection of various machinery, personnel management, budget planning / management, service rate determination, contracting, management of outsourcing companies, etc. Management functions such as maintenance and management, information processing functions for performing installation / improvement / maintenance of computer systems, data input / output tasks, return operations such as return classification / storage, and other tasks for handling claims processing Can be. Among these, functions related to direct logistics activities rather than management tasks include the following functions.
IV. SMART LOGISTICS CENTER DEFINITION
Logistics efficiency is improving as the automation of logistics centers and logistics facilities around the world is progressing. In particular, advanced systems introduced in logistics centers have replaced manpower while carrying out tasks that are difficult for people to do. We collect all the information of the logistics center based on IoT and ICT, utilize and analyze smart technology such as Big Data, and optimize the storage, transportation, unloading, packaging and delivery of products based on the analyzed knowledge, It is a logistics center that can automatically process unmanned by using a robot. Smart logistics centers are becoming the core of new logistics centers because they can integrate management of production, process, logistics management and services.
‘Smart Logistics Center’ enhances efficiency with intelligent operation that incorporates the latest IT technology such as Big Data and IOT. It also contributes to the establishment of managerial logistics operation strategy through decision support function based on logistics data. These smart logistics centers will play a pivotal role in organizing and executing the entire SCM (Supply Chain Management) strategy beyond the warehouses where the former storage was the focus. In addition, robotic technology is attracting much attention in order to reduce the reliance on workforce and increase the speed and accuracy of work. Existing logistics companies are constantly investing in robots to lower the cost of operating the center. In addition to traditional logistics companies, many IT companies are concentrating their efforts on developing robots to provide logistics services. In the future, the logistics center will be equipped with a logistics robot system, which will make it competitive with low human resource dependency and high productivity.
Logistics Advanced countries are already implementing logistics equipment and system upgrading. These recent logistics industries are newly developing with the development of IT technology, which is called new convergence logistics. Numerous companies in Korea are continuously carrying out logistics advancement for new convergence logistics. Below is a list of representative companies.
V. ACTIVEATION PLAN AND EFFECT OF SMART LOGISTICS CENTER
When we look at the cases covered in this study, companies that deal with smart technologies such as smart factories and smart logistics warehouses have in common. It is a system that integrates and manages the information gathered by using various electronic sensors and tags such as RFID, beacon installed in each process and each machine. Therefore, in order for Smart Logistics Center to operate well, it is crucial to collect and manage vast amount of information and to issue orders. Therefore, in this study, smart logistics center to be implemented is classified as smart technology of hardware and software.
MPS is a system that can enhance the efficiency and accuracy by automatically informing the worker of the goods and quantity when applying the electronic tag technology to work such as goods receipt / delivery / inventory survey. That is, the existing Warehouse Management System (WMS) manages the environment in which IOT is implemented in which objects and objects are connected using electronic tags such as Bluetooth and RFID. WMS has the advantage of analyzing real-time asset fluctuation analysis as well as stock position, stock position, arrival time, and storage days. It is possible to efficiently manage all the work (warehousing, warehousing, warehousing, picking, stocking, etc.) performed in the warehouse, thereby reducing inventory management costs and improving the accuracy of the physical inventory. In addition, it utilizes management resources such as warehouse area, worker, and cargo facility with minimum cost to raise service level to customers and maintain storage and inventory situation at appropriate level. The logistics warehouse, which is based on WMS, can further directly involve decision making for customer satisfaction, cost reduction, and productivity improvement, and reflects the overall SCM system by aligning information flow in accounting and real information in the enterprise level. It is a system that must be caught by all because it can be.
It is also important to manage information well, but for machines and people to communicate, it is necessary to visualize information. Currently, there is a one - dimensional management such as cataloging the list of inventory items which was the limit of the warehouse management system. The Smart Logistics Center, which will be built in Busan New Port in the future, should implement a system that can display images of products stored in warehouses through 3D. On-site warehouse managers will be able to manage inventory more efficiently by increasing the visibility of the inside of the warehouse, such as the inventory status by product expiration date, the picking progress status, the inventory status by the number of days stored, and the frequency of shipment. In connection with CCTV, it is possible to remotely monitor real-time warehouse, minimizing damage when a problem occurs. Also, it is necessary to have a system that enables the head office staff to easily grasp the status of local warehousing at a glance without having to visit the site by connecting the central system and the mobile phone and visually showing the logistics warehouse spread over each place. This will be the center point where the head of the head office can quickly connect with the field manager to solve problems effectively in each warehouse.
C) Enabling data security using smart sensors and ISMS
In information gathering and information management through RFID tags and sensors, a step of securing information will be essential. This is to prevent information of error coming in the wrong path and to prevent leakage of important information. Therefore, a system for wirelessly transmitting data to a security server using a protocol that encodes the sensor should be provided. Unauthorized outsiders must form a special algorithm to prevent access to the server. In addition, the certification system of ISMS (Information Security Management System), which is a comprehensive management system such as technical and physical protection measures established and operated for securing the security of information and communication network, should be utilized. It establishes the information protection policy and establishes the scope of the information protection management system and collects and analyzes the data to implement the risk management (risk, vulnerability, asset, threat).
In this study, it is considered that automation of warehouse through stacker crane is one of the most effective equipment of smart logistics center to improve operational efficiency. Stacker crane is a typical equipment of an automatic warehouse. It runs along the rail between the rack structure and the rack structure to the point where the goods are to be shipped. It lifts or descends by the elevator and draws the pallet by using the fork. to be. (Horizontal speed), vertical speed (vertical speed), storage wait time using forks, and retrieval wait time when the article is placed on a conveyor using a fork. Can be divided. In the case of a stacker crane used in a conventional automatic warehouse, a telescopic fork was mounted on a “lifting device" for carrying the product, and only one product could be stored in one row of the stacker crane left and right storage racks while the fork was moved forward and backward.
This not only lowers the storage efficiency, but also increases the economic cost of the equipment. However, the stacker crane of the Smart Logistics Center needs to increase efficiency by introducing a new portable robot device called shuttle. The shuttle, a facility to transport products horizontally, allows storage of multiple products in one row, unlike conventional stacker crane equipment, which only stores one product in one row of storage racks. Conventional stacker crane frame is used as it is, but concept of product storage and operation of warehouse are different from existing facilities by adopting elevator, shuttle, instrument control, product storage rack and operating software. Therefore, this study proposes WMS for the operation of the automatic warehouse system by linking the shuttle, a mobile robot device, and the stacker crane, which is an automation device. It automatically collects barcode or RFID information attached to the pallet required for warehouse automation and automates both the goods loading and unloading system by interworking with shuttle and stacker crane to provide fast service and stable unattended automation operation. It will be a system that can be solved.
Storage of the entire rack will be done through a stacker crane, but other transport equipment such as a forklift is needed if there is a small gap between the rack and the rack, or a rack other than a fixed rack. Until now, a man-operated forklift was commonly used in a warehouse. However, it is necessary to introduce artificial intelligent robots in smart logistics warehouses to be introduced in the future. Robots can be divided into heavy-weight transport robots and light-weight transport robots, depending on their size and movable capability. In the case of the heavy transport robot, the maximum movable weight is 500kg. A lightweight transportation robot is a robot capable of picking a small amount and guiding a worker to a place where goods are located. One of the most suitable models for heavy-duty transport robots is Amazon’s ‘Kiva’ transport robot. The Kiba robot features fast picking while transporting the shelf itself. In addition, ClearPass Robotics uses ‘OTTO’, which is a larger transportation robot than Kiba. The robot, which can carry loads of about 1500kg, uses the laser to grasp the terrain and move it so that it can be used directly from the general warehouse without any special guidance device.
I think drones will be the best for lightweight transportation robots. Drones have the advantage of being able to perform their duties according to their own environment judgment without any fixed line or equipment. It is not to connect to logistics center from customer like door-to-door, but to introduce drones for more accurate and quick movement of goods in smart logistics center. During picking operation, if a picking operation is required for defective or small quantities, the movement of a large machine is inevitably time consuming and economical. If you use the drone, it will be possible to pick out as fast as you need. In the future, these transportation robots will move with the control of the central computer through secure Wi-Fi connection, and should be able to operate efficiently in a narrow space in the warehouse. I think that robots that recognize the QR code of the warehouse floor by the camera and recognize the current position and the infrared-based obstacle detection function will contribute to the more efficient flow of the logistics. Transport robots implemented in Smart Logistics Centers should have the ability to be tired and moveable and to have sophisticated picking ability like human. These robots can be used not only for quick picking but also for stock check and replenishment at the same time, maximizing work efficiency.
On the conveyor belt that packages or inspects the goods, it is necessary to read out the information of the barcode or RFID in order to perform a more accurate inspection than the person. It may also be necessary to modify the transport equipment to prevent damage to the packaged goods.
It is possible to reduce the damage of goods by equipping cross-belt equipment that horizontally moves the cargo on the conveyor belt and minimizes impact. It is necessary to introduce a technology of recognizing the information on the transportation route barcode of the moving cargo by implementing a five-sided camera on the conveyor belt. The simultaneous X-ray cargo system enables the user to quickly identify and classify the goods by checking X-rayed items and their information such as invoice number, customer name, and price.
The smart logistics center, which will be newly established in the future, should also be able to manage the goods well and deliver goods to the end. The introduction of such an automatic classifier and X-ray cargo implementation system will enable the rapid and safe handling of large quantities of cargo.
III. CONCLUSION
The German Merkel government announced ‘Industry 4.0’ for manufacturing innovation in March 2012. Industry 4.0 became the foundation of the Smart Factory by constructing a system to digitize and control the processes of product such as development, production and service. Smart Factory can be defined as a place where various parameters and data can be predicted based on the system that collects and manages the information by attaching the wireless network sensor to all equipment and machinery in the factory. Developed countries such as the US, France, Germany, and Japan, which have pursued the tea industry revolution, have only a few Smart Factories.
In Korea, we are promoting the Smart Factory Industry by announcing the 'Manufacturing Innovation 3.0 for Creation Economy Implementation' strategy. This ‘Manufacturing Innovation 3.0 Strategy for Creation Economy’ is a fusion of IT, SW, , It is the government’s strategy to improve the manufacturing of small- and medium-sized enterprises through Smart Factory Promotion Team by promoting the smartization of 10,000 plants by putting 1 trillion won into the joint venture by 2020. IT & Future Strategy Report of Korea IT Promotion Agency 2014. 5. 30 Industry 4.0 and Manufacturing Creation Economic Strategy Report reveal that the environment surrounding the manufacturing industry is rapidly changing and the significance is re-emerging along with manufacturing revival. Smart Factories are focused on the development of infrastructure technologies such as Internet of Things, Cyber-Physical System (CPS) and sensors, and ICT-based smartization is applied to all kinds of smart phones, smart meters, smart cities, smart grids. This has resulted in increased production, safety, speed, and efficiency. The study suggested applying these techniques to logistics centers.
Busan New Port is located on the main route linking Europe and the Americas. With more than 300 regular routes per week, it has established links with the rest of the world and has secured land-sea transportation facilities such as roads, railways and airports. Air transportation system. However, due to the high growth of Chinese ports, the growth rate of trade volume has been drastically decreasing over the years. It is indispensable to raise the competitiveness of Busan New Port in order to solve the above problems and to increase the rate of increase in the volume of traffic in Busan Port. In order to enhance the competitiveness of Busan New Port, we will build a Smart Logistics Center like Smart Factory.
Smart technologies continue to evolve, and scholars see 2020 as the fourth industrial revolution. Accordingly, it is necessary to change the port of Busan New Port. Hanjin Shipping, which was a strong domestic company, is in a crisis of collapse, and the volume of trade volume continues to decrease. As a countermeasure against these crises, we will be able to recover international competitiveness and freight volume with the smartization of Busan New Port Logistics Center and move forward as the leading city of future logistics business.